Rust Grip
Lead-Based Paint Encapsulation
For Rusted Metal
Before
After
Rust Grip Advantages
- Approved Encapsulant - Passed ASTM E 1795
- Single Component - No mixing part A & B
- Fast Cure - Humidity Accelerates Curing
- Surface Tolerant - Minimal Surface Preparation
- Easy To Apply - Brush, Roll or Spray
- Save $$$ - On Disposal Of Hazardous Waste
- Save $$$ - No Need to Hire a Hazardous Waste company
- Save Time - On Application And Clean-Up
- Saves On Relocation Costs - For Residents/Occupants
- Non Toxic - Low VOC Formulation
Lab Testing
Lead Paint Case Studies
Gadsden CSX Truss Bridge
Inspection of structure conducted March 2017. Project completed in 2009. Applied over lead based paint, with only hand tooling and 5,000 psi power wash. Design was approved and stamped by U.S. Army Corp. of Engineers.
Barefoot Tourat Truss Bridge
Inspection of structure conducted March 2018. Project completed in 2010. Applied over lead based paint, with only hand tooling and 5,000 psi power wash. Design was approved and stamped by U.S. Army Corp. of Engineers.
Lab Testing
Passed ASTM E-1795
Standard specification for non-reinforced liquid coating encapsulation products for leaded paint in buildings
ASTM D5894 – Cyclic Salt Fog Test @ 6 mils DFT
10,000 hours - Perfect 10 out of 10
Some blistering is noted on the edges of the two coupons, however, this is due to the edge effect and not due to a deficiency in the coating.
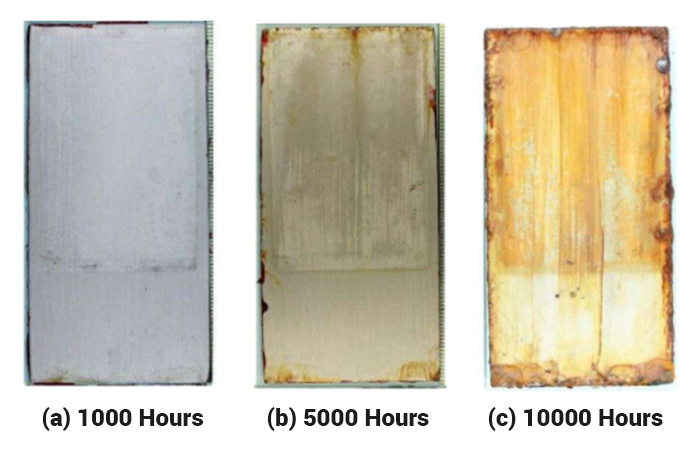
Passed ASTM E-1795
Standard specification for non-reinforced liquid coating encapsulation products for leaded paint in buildings
ASTM D5894 – Cyclic Salt Fog Test @ 6 mils DFT
10,000 hours - Perfect 10 out of 10
Some blistering is noted on the edges of the two coupons, however, this is due to the edge effect and not due to a deficiency in the coating.
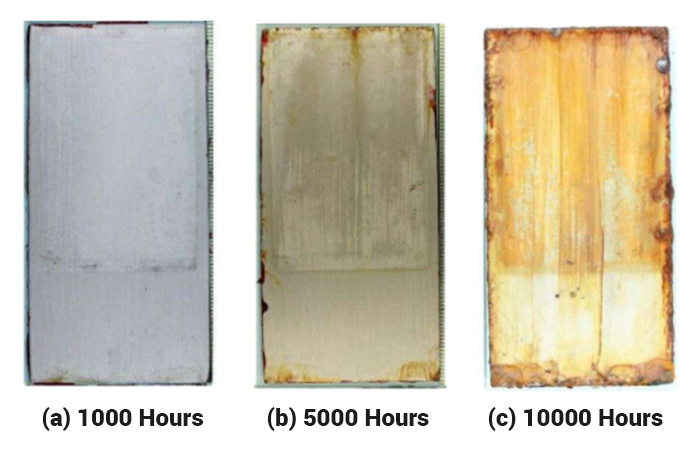
No Sandblasting Required or
Lead Dust Containment issues
- ASTM E1795
Standard Specification for Non-Reinforced Liquid Coating Encapsulation Products for Leaded Paint in Buildings
Rust Grip Sole Specified for
Lead Based Paint Encapsulation
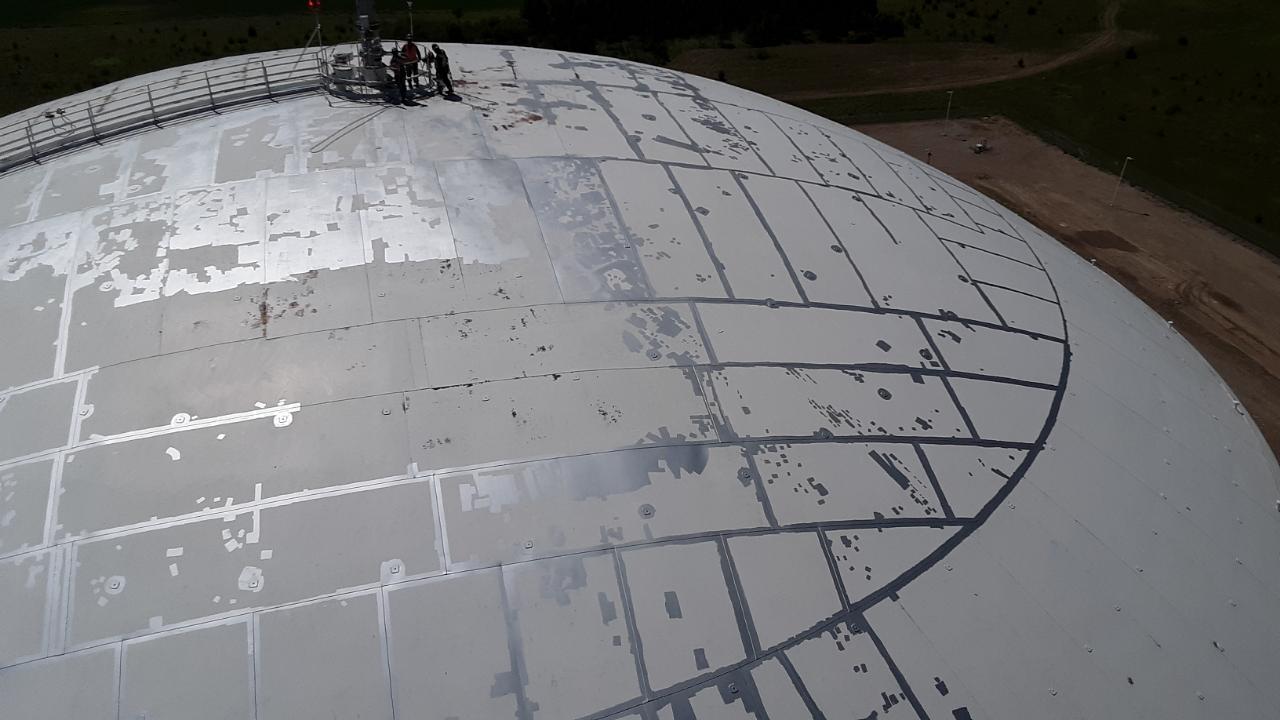
Army Corp. of Engineers
Rust Grip - Best Coating Tested
Before
After
Lead Paint Case Studies
Gadsden CSX Truss Bridge
Inspection of structure conducted March 2017. Project completed in 2009. Applied over lead based paint, with only hand tooling and 5,000 psi power wash. Design was approved and stamped by U.S. Army Corp. of Engineers.
Barefoot Tourat Truss Bridge
Inspection of structure conducted March 2018. Project completed in 2010. Applied over lead based paint, with only hand tooling and 5,000 psi power wash. Design was approved and stamped by U.S. Army Corp. of Engineers.
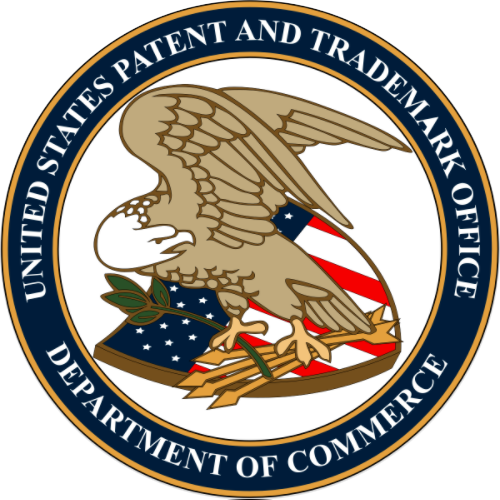
US PATENT 5,695,812
Method for Abating Bio-Hazardous Materials
Found in Coatings Such as Lead Based Paint
Certifications
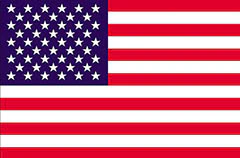
Made in USA
Technical Data
Technical Data
Description
RUST GRIP is a tough, single component moisture cure polyurethane coating, loaded with metallic pigments for additional strength. In most cases, abrasive blasting is not required. RUST GRIP is designed to resist chemical solvents and acid splashes; it can be used as a primer or a one coating system.
Application
RUST GRIP can be applied to metal, concrete, masonry and wood. Application can be by airless sprayer or brush/roller. Application thickness depends on surface profile.
Physical Data
- Solids: By Weight 62.2% / By Volume 51.4%
- Cures by absorbing moisture from in the air
- Weight: 9.4 lbs per gallon
- Shelf life: 3 years if unopened under normal conditions
- Resistant to most solvents, chemicals, and some acids
- VOC Level: 380 grams/liter
- Max. Surface Temp. when applying: 150°F
- Min. Surface Temp. when applying 50°F
- Min. Surface Temp. when applying 10°C
- Max. Surface Temp. after curing: 325°F
- Max. Surface Temp. after curing: Constant or greater than 163°C
Description
RUST GRIP is a tough, single component moisture cure polyurethane coating, loaded with metallic pigments for additional strength. In most cases, abrasive blasting is not required. RUST GRIP is designed to resist chemical solvents and acid splashes; it can be used as a primer or a one coating system.
Application
RUST GRIP can be applied to metal, concrete, masonry and wood. Application can be by airless sprayer or brush/roller. Application thickness depends on surface profile.
Physical Data
- Solids: By Weight 62.2% / By Volume 51.4%
- Cures by absorbing moisture from in the air
- Weight: 9.4 lbs per gallon
- Shelf life: 3 years if unopened under normal conditions
- Resistant to most solvents, chemicals, and some acids
- VOC Level: 380 grams/liter
- Max. Surface Temp. when applying: 150°F
- Min. Surface Temp. when applying 50°F
- Min. Surface Temp. when applying 10°C
- Max. Surface Temp. after curing: 325°F
- Max. Surface Temp. after curing: Constant or greater than 163°C